- Hogar
- Soluciones
- Application of SF81 Using on Injection Molding Machine Control System
Application of SF81 Using on Injection Molding Machine Control System Solución
Descripción general
- Descripción general
- Características y Beneficios
- Productos relacionados
- Casos relacionados
- Noticias y eventos relacionados
- Soluciones relacionadas
- Contacta con nosotros
Application of SF81 Using on Injection Molding Machine Control System Solución
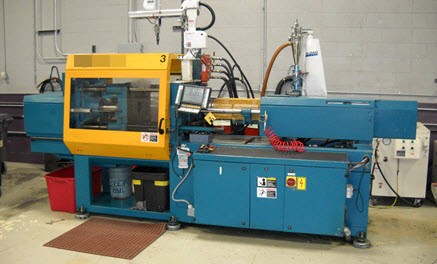
Características y Beneficios
For a long time, plastic has already become one of the major materials for industrial, agricultural and civilian use. Injection molding machine, a kind of special plastic molding machinery, is of common use for creating various kinds of plastic items. Injection molding machine uses the thermal plasticity feature of plastic after proper heating and melting to create different varieties of profiles and plastic products.
Part 1. Great Advantages of Adopting Veichi SF81 on Injection Molding Machine System
As a statistic of our customers shows, adopting variable speed drives on injection molding machine system has a lot of advantages, including:
1. Save energy
2. Improve productivity and product quality
3. Reduce oil pollution and noise pollution
4. Extend the life span of injection molding machines…
As there is a lot of great benefits of using variable speed drives on the injection molding machine control system, so it has been applied in more and more plastic processing plants.
Part 2. Main Process Steps of Injection Molding Machines
Before we introduce the energy-saving principle of injection molding machines, firstly we will discuss its brief process steps which are as follows:
1. The lock mode: template quickly approaches to the stationary platen, when confirmed that there is no foreign material exists, the system will switch to high pressure mode to lock the template.
2. Injection units moving forward: the nozzle and mold close together.
3. Injecting: injection screw injects the melt material on the front-end of feed cylinder into the mold cavity with a certain pressure and speed.
4. Packing and cooling process: through the actions, it makes the melt material inside the mold cavity cool and formed.
5. Pre-plastic: traditionally, the hydraulic motor drives the screw and draws back, then plastic particles added to the hopper are pushed forward for pre-molding. The screw stops when retreating to the predetermined position, and then gets ready for the next injection.
6. Injection table draws back and open mold.
7. Eject created plastic product.
Part 3. Why Traditional Injection Molding Machine Control System is Not Energy-saving
On traditional injection molding machines, these actions are completed by the hydraulic system: the pressure and flow generated by the oil pump and valves provides the required impetus and moving speed of cylinders and hydraulic motors.
As what you know:
The output frequency of oil pump is: "Pt = p * qt = p * V * n".
The theory pump torque is: "Tt = 1 / 2pi * p * V".
In the above formulas, "p" stands for pressure, "qt" stands for flow, "V" stands for pump displacement, "n" stands for pump rotating speed, and "pi" is 3.14.
According to the formulas, you can get: "Pt = 2pi * Tt * n".
If we ignore the energy loss during the process of converting mechanical energy into hydraulic energy, then it can be approximately considered that the output power, electric motor output torque and rotating speed is proportional. Thus it can be seen, when the system requires low flow, the system required power is very low. But the fact is that we cannot reduce the motor rotating speed (in order to reduce the flow) according to the actual requirements, as the motor is always running on power frequency – 50Hz. Thus redundant hydraulic oil flows back into the tank via the relief valve, resulting in energy waste.
Part 4. Working Principle of Veichi SF81 Injection Molding Machine VFD
1. Energy-saving.
According to the special application requirements, Veichi has developed SF81 servo controller VSD for injection molding machines. SF81 adopts system pressure, single or double closed loop flow control modes. It can enable the hydraulic system to supply oil in accordance with the actually required flow and pressure. It overcomes the high energy consumption caused by high pressure overflow of common fixed displacement oil pump system. During the process of pre-molding, mold, plastic injection and other high flow sessions, SF81 lets the motor work at required speed. During the process of packing, cooling, and other low flow sessions, SF81 lets the motor run at low speed and zero speed. Therefore, it greatly reduces the actual energy consumption of oil pump motors.
2. Enhance productivity of injection molding machines.
Besides, Veichi SF81 series injection molding machine servo controller features fast response speed, so the flow and pressure rising time is as fast as 50ms. Therefore, it greatly improves the response speed of the hydraulic system, reduces the action transition time, and speeds up the running tempo of the whole machine. During the automatic running status, the system pressure will drop instantly when a valve is opened, then the servo system can quickly supplement oil within 50ms to restore preset pressure value. SF81 ensures the hydraulic system with improved features like high regulation accuracy, high repeat accuracy, material saving, and low oil temperature. Besides, SF81 is simple and convenient in installation and operation.
3. Improve product quality.
a. Disadvantages of using common VVVF control
(1) Under common VVVF (the abbreviation of variable voltage variable frequency) speed control mode, the motor flux is kept constant when the proportion rate between frequency and voltage is kept constant. In this mode, there is speed feedback device, so it cannot accurately reflect the true speed of the motor. As the motor is three-phase asynchronous motor, there is deviation between the actual rotor speed and the stator rotating magnetic field, the slip ratio changes when the external load changes, but the drive cannot compensate for this, so the oil pump speed changes, causing deviation in flow and decline in the product quality.
(2) There is another drawback of using VVVF control: when the output frequency is 0Hz, the theoretical output voltage is 0V, the motor stator flux is approximately 0?m, thus it affects the starting characteristics of the motor causing slow acceleration response speed. As injection molding machine requires instantaneous high pressure, high flow during some actions like injection, if we use open loop general purpose frequency inverters, it is difficult to meet the required fast rising pressure response, affecting the injection pressure.
b. Why SF81 is the Best Choice for Controlling Injection Molding Machine
Veichi SF81 adopts rotor field oriented control theory – it transforms the coordinate of induction motor current to make the control equivalent to DC motor control. Under three-phase coordinate system, the stator alternating current "ia", "ib", "ic" converts between three phase and two phase, which is equivalent to alternating current "ia" and "i?" of two-phase static coordinate system, then through rotor flux oriented rotated transformation, it is equivalent to direct current "it" and "im" of synchronous rotating reference frame. "im" is equivalent to the excitation current of DC motor, it is equal to armature current which is proportional to the torque in DC motor. Because no matter what state the motor is, running or stationary, its excitation current "im" always exists. Through adjusting armature current "it" individually, we can control the magnitude of the torque to make the induction motor is always in a high dynamic state. It only takes 50ms to accelerate from 0rpm to 1000rpm, which makes ups the drawbacks of poor dynamic performance of variable voltage variable frequency control system, so it ensures the high following performance of injection molding machine operating cycle.
Through the system self-learning to motor, it can measure the stator resistance and inductance accurately, so that it can keep the excitation current constant, then it makes the flux constant. The motor slip frequency
, when the flux
is constant, the slip frequency is proportional with the torque in dynamic status of vector control system, so the stator magnetic field frequency
is rotor frequency what is controllable. This means that when the load fluctuates, the VFD drive control section can quickly calculate the actual slip frequency , thereby giving a precise rotational frequency to the stator to remain constant motor speed. It effectively increases the running stability of motor when load changes.
In summary, Veichi SF81 provides a professional control solution to injection molding machines as it is of high dynamics, good stability, easy installation and simple debugging.