- Hogar
- Soluciones
- VFD Troubleshooting
VFD Troubleshooting Solución
Descripción general
- Descripción general
- Características y Beneficios
- Productos relacionados
- Casos relacionados
- Noticias y eventos relacionados
- Soluciones relacionadas
- Contacta con nosotros
VFD Troubleshooting Solución
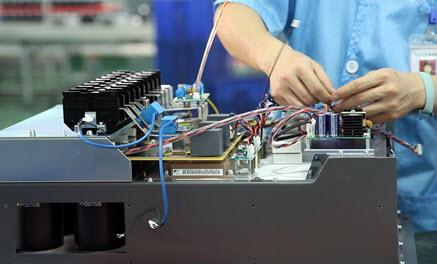
Características y Beneficios
During the process of maintaining VFD drive, we may come across various kinds of problems such as circuit problem, incorrect parameter settings, mechanical faults as well as VFD faults. If the problem is caused by VFD fault, so how can we do the VFD troubleshooting? In this article, we will introduce about how to troubleshoot VFD drives step by step.
Step-by-Step VFD Troubleshooting Guide
1. Static Testing
a. Test rectifying circuit
Find the P and N terminal of DC power supply inside the VFD, and then navigate to the multimeter to adjust the resistance to X10, connect the red hand of multimeter to P terminal, connect the black hand of multimeter to R, S and T in turns, it should have about dozens of resistance and be balanced. To the contrary, please connect the black hand of multimeter to the P terminal, connect the red hand of multimeter to R, S and T one by one, and there should be a nearly infinite resistance. Then please connect the red hand of multimeter to the N terminal, repeat the above steps, and it should have the same results. If you have the following result, we can judge that the circuit is abnormal: (1) resistance three phase imbalance, which implies the rectifier bridge failure. (2) When the red hand of multimeter is connecting to P terminal, if it has infinite resistance, then it proves that there is failure in rectifier bridge or starting resistor.
b. Test the inverter circuit
Connect the red hand of multimeter to P terminal, connect the back hand to U, V and W, and there should have about dozens of resistance and the resistance is basically the same. To the contrary, it should be infinite resistance. Connect the black hand of multimeter to N terminal, repeat the above steps and we should get the same result. Otherwise, it should have failure in inverter module.
2. Dynamic Testing
We can only perform the dynamic testing (test machine with power supply) when the static testing results are normal. Before it, please pay attention to the below points:
a. Before power on, please make sure the input voltage in correct. If we connect the 220V VFD to 380V power grid, the burn-off phenomena (burn off capacitor, piezoresistor, modules and etc.) will happen.
b. Please inspect whether the transducer broadcast port is properly connected or not, whether the connection is loose or not. Abnormal connection may cause VFD failures, severe burn-off and other situations.
c. Power on to check the fault display for the fault reasons.
d. If it displays no fault, firstly check whether the parameters settings are normal. And restore parameters, start VFD at unload condition to test the output voltage value of U, V and W phase. If the phases lose, unbalanced three phases and other results occur, and then there should have failure in module and driver board.
e. Under the condition of normal output voltage (without phase lose and unbalanced phase), please troubleshoot the VFD with full load.
3. Failure Diagnosis
a. Rectifier module is damaged.
Generally, it is caused by power grid voltage and internal short circuit. If checked that there is no internal short circuit, please replace the bridge rectifier. When troubleshoot the VFD failures on the scene, we should focus on checking the power grid such as voltage, whether there is welding machine or other equipments (these equipments pollute the power network).
b. Inverter module is damaged.
Usually, it is caused by motor failure or drive failure. After fixing the drive circuit and measuring that the driving waveform is in good condition, then can we replace the module. After the replacement of driver board on the scene, please check the motor and connection cable. After we make sure that there is no failure, then start VFD.
c. Powered on with no display
Usually it is caused by damaged switch power supply, damaged soft charging circuit, damaged starting resistor or damaged panel.
d. Powered on and it displays overvoltage or under voltage
Generally, it is caused by input phase lost, aging circuits and damp circuit boards. To perform VFD drives troubleshooting, please inspect the circuit and test points to replace the damaged parts.
e. Powered on and it displays current or earth short circuit
Generally, it is caused by damaged current detecting circuit such as hall elements, amplifiers and etc.
f. It displays overcurrent when start
Usually, it is caused by damaged drive circuit or damaged counter module.
g. Voltage is normal at no load status. However, it displays overload or overcurrent at load status.
Generally, this failure is caused by improper parameter setting, aging driving circuit or module damage.
If you need more detailed information about VFD troubleshooting, please contact us and our technical support will reply you in details as soon as possible. If you need frequency inverters such as vector drives, tension control inverter or others, Veichi will provide you high quality VFDs at wholesale price.