- Hogar
- Soluciones
- Application of Veichi AC90 Frequency Inverter on Dye Jigger
Application of Veichi AC90 Frequency Inverter on Dye Jigger Solución
Descripción general
- Descripción general
- Características y Beneficios
- Productos relacionados
- Casos relacionados
- Noticias y eventos relacionados
- Soluciones relacionadas
- Contacta con nosotros
Application of Veichi AC90 Frequency Inverter on Dye Jigger Solución
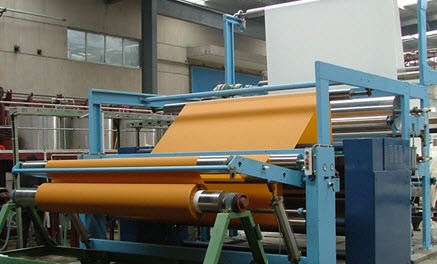
Características y Beneficios
Abstract: In dye jigger control, the PLC with double frequency inverter is simple in configuration and excellent in control performance, which can reduce system cost. This article describes the application details of AC90 series high-performance vector inverter on dye jigger.
1. Introduction
Currently, in textile processing market, cloth dyeing is an important step. Relevant textile processing such as fabric bleach, color and surface pressure grinding can be realized by Dye jigger. Dye jigger control requires automatic counting, automatic turning and auto-stop (emergency stop and stable) and other functions. Throughout the processing, the tension and speed of the cloth should be constant, which requires a higher level of control for the entire control mechanical transmission system.
2. Dye Jigger Processing
The mechanical outline drawing of Dye jigger is as follows:
The jigger uses two three-phase induction motors and the reducer drags the roller to do the cloth dyeing. When the dye jigger works, one central axis of curl controls the system. The finished cloth would first be rolled onto one roller mounted, and there is proximity switch for counting on the drum shaft (ie, the proximity switch generates a pulse when rolling a cycle), then the tension controller of the dye jigger would count the value of the next piece of cloth.
When up rolling is over, manually pull one end of the cloth through the dye cell and shaft to another roll and wrap it tightly, then start the dye jigger and the fabric dyeing starts. In this case the two rollers move in the same direction, and the pulling tension should be constant and the time when the cloth passes through the dye should consistent. This is a drive control system without line speed feedback or linear speed feedback. Therefore, the output frequency and the output torque of the unwinding frequency inverter should be adjusted unwinding inverter to achieve the unique requirements.
3. Dye Jigger Control
Dye jigger control diagram is as follows:
PLC is the main controller of the dye jigger and touch screen is the user interface, which mainly completes the settings of cloth tension, line speed, cloth thickness, and the calculation of running frequency of the winding motor and the output torque of the unwinding motor as well as the control of automatic U-turn, automatic parking and other related logic operations. 485 communication (Modbus RTU communication protocol)is adopted between the drive and the controller. From the control schematic: two same frequency drives work in the VC with PG mode. PLC controller would record the number of cloth when the cloth is on the roller and then the cloth thickness would be measured by operators, and this measured value would be inputted to the controller to accurately calculate the diameter of the roller based on the thickness and number of turns of the cloth. Real time radius can be easily obtained by this thickness integral method and the error is small. PLC can accurately calculate the corresponding torque (winding motor) and matching frequency (unwinding motor) based on real-time turning radius, user-set tension and line speed. And the calculated results would be transmitted through 485 serial communications to AC90 frequency inverter as the basic parameters of the winding motor and the unwinding motor, thus ensuring the constant linear speed and constant tension control.
4. System Features
According to the work principle of the dye jigger, the motor on unwinding side is always in power generation state and the usual practice method is using braking resistor and braking unit to consume the electricity power in the form of heat. For dye jigger, which works in power generation state for such a long-term, this way is a great waste of energy and the electrical control cabinet space is also occupied. Frequency converters especially AC90 series high-performance vector inverter can easily support the common DC bus, and when two inverter DC buses directly in parallel, when the dye jigger works, the power generated during unwinding braking would be transmitted back to the winding motor by the parallel buses, so that the power can be fully used, which greatly improves the efficiency of energy. But in fast stop when two motors are in power generation state, and one of the frequency converter is still in parallel with a braking resistor, of which the work time is short and the energy consumption is small, mainly to prevent over voltage fault when parking the drive system.
5. Conclusion
Compared with DC speed control system, AC90 high-performance vector control inverter has higher performance for controlling the dye jigger, which provides an excellent solution for the product upgrading of dyeing industry.